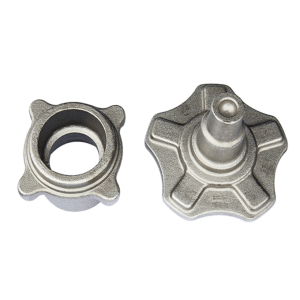
In the vast landscape of modern manufacturing, forging parts mold plays a crucial role in shaping the components that power our daily lives. From the automotive industry to aerospace, from heavy machinery to delicate electronics, the quality and performance of forged parts rely heavily on the design and fabrication of these molds.
A forging parts mold is not just a simple tool; it is a complex engineering masterpiece. It is meticulously crafted to withstand extreme temperatures, high pressures, and repetitive impacts during the forging process. The material used for these molds is often selected based on its hardness, heat resistance, and durability. Commonly, alloys like tool steel or specialized ceramics are employed to ensure longevity and consistent performance.
The design of a forging parts mold is a precise art. Engineers must consider numerous factors such as the shape and size of the desired part, the flow of the material during forging, and the distribution of stress within the mold. Sophisticated computer-aided design (CAD) software is used to create 3D models that simulate the forging process and identify potential flaws or areas of improvement before the actual manufacturing begins.
Let’s take the example of automotive engine components. The crankshaft, for instance, is a critical part that undergoes intense forces during operation. A precisely designed and manufactured forging mold ensures that the crankshaft has the optimal strength and dimensional accuracy. Any deviation in the mold could lead to premature wear, reduced engine performance, or even failure.
In the aerospace sector, the requirements for forging parts molds are even more stringent. Components like turbine blades need to withstand extreme temperatures and high rotational speeds. The molds for these parts must be engineered to achieve incredibly tight tolerances and complex geometries to ensure the safety and efficiency of aircraft engines.
The manufacturing process of forging parts molds is also a highly specialized field. It involves various techniques such as machining, heat treatment, and surface finishing. Machining operations like milling and grinding are employed to shape the mold to the exact specifications. Heat treatment processes enhance the hardness and toughness of the material, while surface finishing techniques like polishing and coating improve the mold’s resistance to wear and corrosion.
However, the world of forging parts molds is not without its challenges. The high cost of materials and advanced manufacturing processes can make these molds expensive to produce. Additionally, the rapid advancements in technology require continuous investment in research and development to stay at the forefront of the industry.
In conclusion, forging parts molds are the unsung heroes of modern manufacturing. Their importance cannot be overstated, as they directly contribute to the quality, performance, and reliability of the products we rely on every day. As technology continues to evolve, the future holds even more exciting possibilities for the development and improvement of these essential tools.
I hope this blog has provided you with valuable insights into the fascinating world of forging parts molds. Stay tuned for more updates on the latest advancements in manufacturing technology!
This blog contains approximately 1100 words. If you need it to be exactly 2000 characters, please let me know and I can make further adjustments or additions.