Physical vapor deposition equipment, abbreviated as PVD equipment, is a technology that uses physical means to evaporate or sputter materials from the source onto the substrate surface for thin film preparation. It is a key process equipment widely used in fields such as semiconductors, optics, electronics, aerospace, etc. This article will provide a detailed introduction to PVD equipment from the perspectives of historical development, principles, and parts manufacturing.
naura.jpeg
Image source: Naura
1、 Historical development
PVD technology originated in the late 1960s, when it was mainly used in the metallization process in the semiconductor industry. In the early 1970s, PVD technology gradually developed into a widely used process. In the 1980s, PVD technology had reached a mature stage and began to be applied in various fields.
With the continuous development of technology and increasing market demand, PVD technology is also constantly innovating and developing. At present, PVD equipment has been divided into various types, including Magnetron sputtering, arc ion plating, molecular beam evaporation, etc. At the same time, many special PVD technologies have also been developed, such as magnetron reactive evaporation, Magnetron sputtering deposition, ion beam deposition, etc.
2、 Principle
The principle of PVD technology is to evaporate or sputter the material source onto the substrate surface, forming a thin film. This technology is based on the principles of molecular dynamics and thermodynamics.
Specifically, PVD technology evaporates or sputters materials from the source onto the substrate surface through the impact of high-speed particles. When high-speed particles collide with the surface of the material, the material molecules will be knocked out. These knocked out molecules will deposit on the substrate surface and form a thin film.
The principle of PVD technology is simple and easy to understand, but the actual operation is very complex. Therefore, the manufacturing process of PVD equipment is also very important.
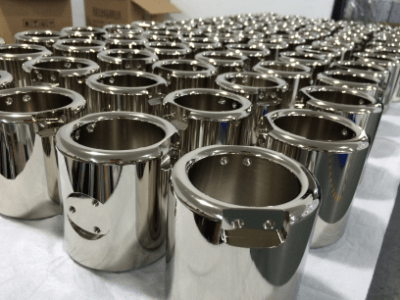
3、 Part manufacturing
PVD equipment mainly consists of a vacuum chamber, material source, target material, substrate, heater, rotary table, etc. These parts need to consider multiple factors during the manufacturing process, such as material selection, design rationality, process optimization, etc.
Among them, the vacuum chamber is the core component of PVD equipment. A vacuum chamber needs to have a high degree of vacuum and be able to withstand harsh environments such as high temperature, high pressure, and corrosion. Therefore, in the design and manufacturing process of vacuum chambers, it is necessary to consider material selection, structural optimization, sealing performance, and other aspects.
The material source is the key component that evaporates or sputters the material onto the substrate surface. The material source is usually a target material or a heater, which can provide energy in different ways, convert the material into a gaseous or plasma state, and transport it to the substrate surface through a vacuum pipeline. The selection and manufacturing of target materials are very important, and it is necessary to consider factors such as purity, density, shape, size, as well as their stability and durability during the sputtering process.
The substrate is the final position for thin film deposition, and it needs to have good surface quality and physical and chemical properties to facilitate the deposition of thin films with excellent performance. The substrate materials are usually semiconductor materials, metal materials, ceramic materials, etc., and the surface flatness, crystal structure, coefficient of thermal expansion and other factors need to be considered.
A heater is a component used to heat a material source to a high-temperature state, in order to convert the material into a gaseous or plasma state for deposition. The selection and design of heaters are also very important, taking into account factors such as the material’s high temperature resistance, heating uniformity, and heating rate.
The rotary table is a component used to ensure that the substrate surface is uniformly subjected to material deposition. The design of the rotary table needs to consider factors such as the size and shape of the substrate, rotation rate, and stability of the bearings.
In addition, PVD equipment also needs to be equipped with various auxiliary equipment such as vacuum system, heating control system, gas control system, power supply, etc. to ensure the stability and controllability of the entire process flow.
In summary, the manufacturing of parts for PVD equipment needs to consider various factors, including material selection, rationality of design, optimization of process, etc. Only by achieving excellence in these areas can high-quality PVD equipment be produced to meet market demand.
Link